Pyrometers are stationary infrared temperature sensors and infrared temperature measuring devices for non-contact temperature measurement that are usually used in industrial applications.
(The description of portable infrared thermometers can be found here)
In a pyrometer, the electromagnetic radiation emitted by the object being measured in the infrared range is converted into a measured value, which is given out as an output signal.
Pyrometers only passively absorb the infrared radiation from the measured object and do not emit any radiation to the measured object. If the emissivity setting is correct, the measured temperature value corresponds to the surface temperature of the object being measured.
Pyrometers are manufactured for a wide range of applications in various designs and configurations that differ in terms of optics, technology, size, shape, temperature measuring range, spectral range and output signal.
Two-part infrared pyrometer
Two-part infrared pyrometers consist of a sensor head which is connected to an evaluation/controller unit.
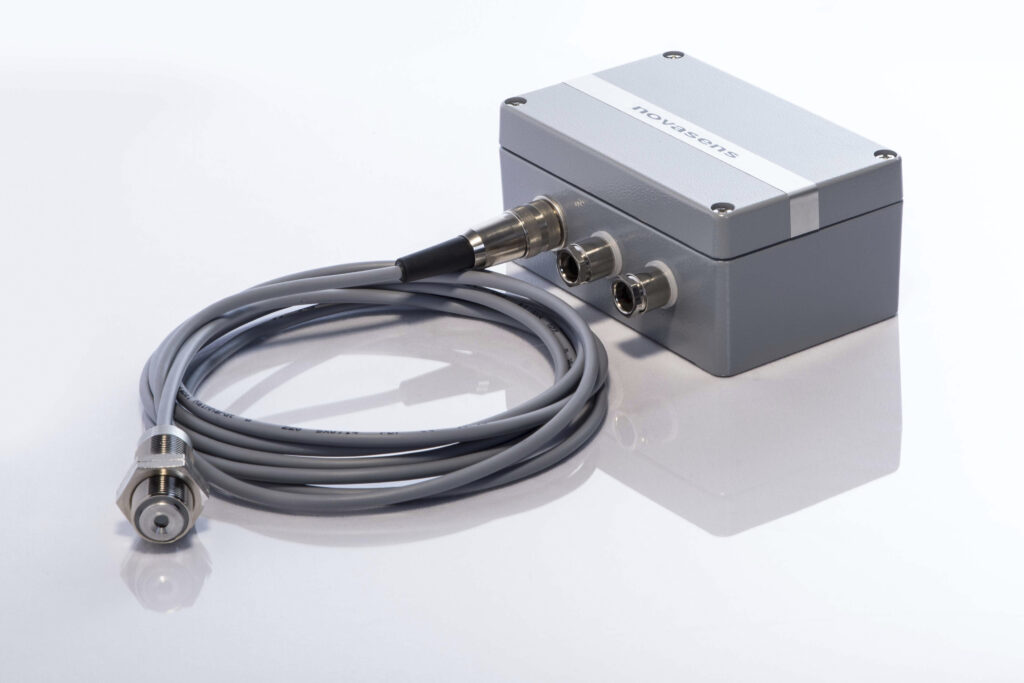
One-piece infrared temperature sensor
One-piece infrared temperature sensors have the sensor electronics integrated in the sensor head and no longer require an evaluation/controller unit.
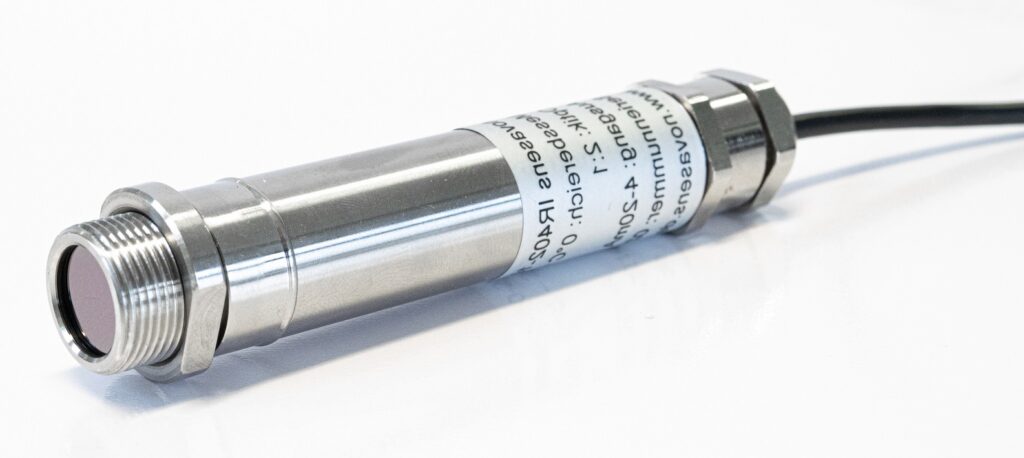
How a pyrometer works
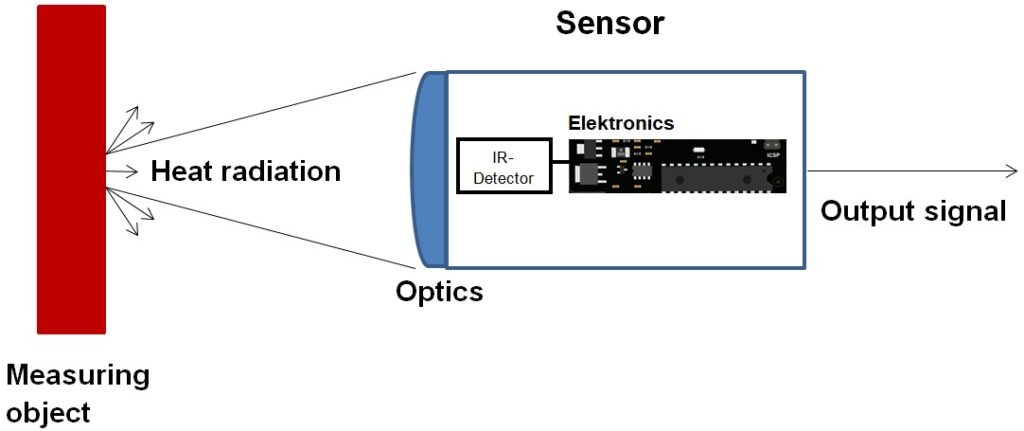
1. the measurement object emits electromagnetic radiation in the infrared range. The pyrometer’s optics record a specific area of the measurement object as a measurement spot.
2 The pyrometer’s optics concentrate the infrared radiation onto the IR detector.
3. the IR detector converts the infrared radiation from the measurement object into an electrical signal and passes this on to the pyrometer electronics.
4 The pyrometer electronics convert the electrical signal into a temperature value.
5. the determined temperature is output as an analog sensor standard output signal or as a digital signal.
Emissivity correction / setting the emissivity in the pyrometer
For a pyrometer to measure the temperature correctly, the emissivity of the material of the object to be measured must be known and set in the pyrometer.
Especially in the non-contact temperature measurement of metals and other measurement objects with a low emissivity, an incorrectly set emissivity is a frequent source of error when strongly deviating measurement results occur.
It should be noted that emissivities are not absolute values, but depend on other factors. You can find an overview of the most common materials and the corresponding emissivity in our emissivity wiki page and our emissivity table.
Spectral range
Pyrometers for non-contact temperature measurement of various materials are available in different spectral ranges.
The novasens IR702 pyrometer shown below measures in a spectral range of 2.2 µm and is therefore suitable for non-contact temperature measurement in the metal and steel industry. The table below gives a simplified overview of the spectral ranges. It should be noted that for non-contact temperature measurement of metals and glass, the spectral range also depends on the temperature range in which the measurement is to be taken.
Spectral range | Field of application |
8-14 µm | Non-contact temperature measurement of paper, laminate, water, textiles, plastics, leather, tobacco, liquids, pharmaceuticals, chemicals, rubber, coal, asphalt, foodstuffs, pharmaceutical products, coated metals |
2,2 µm | Measurement of metals in the low temperature range |
2,3 – 5,0 µm | Use in glass production, glass refinement, further processing |
0,8 – 3,9 µm | Iron and steel production, forging processes, metal finishing processes |
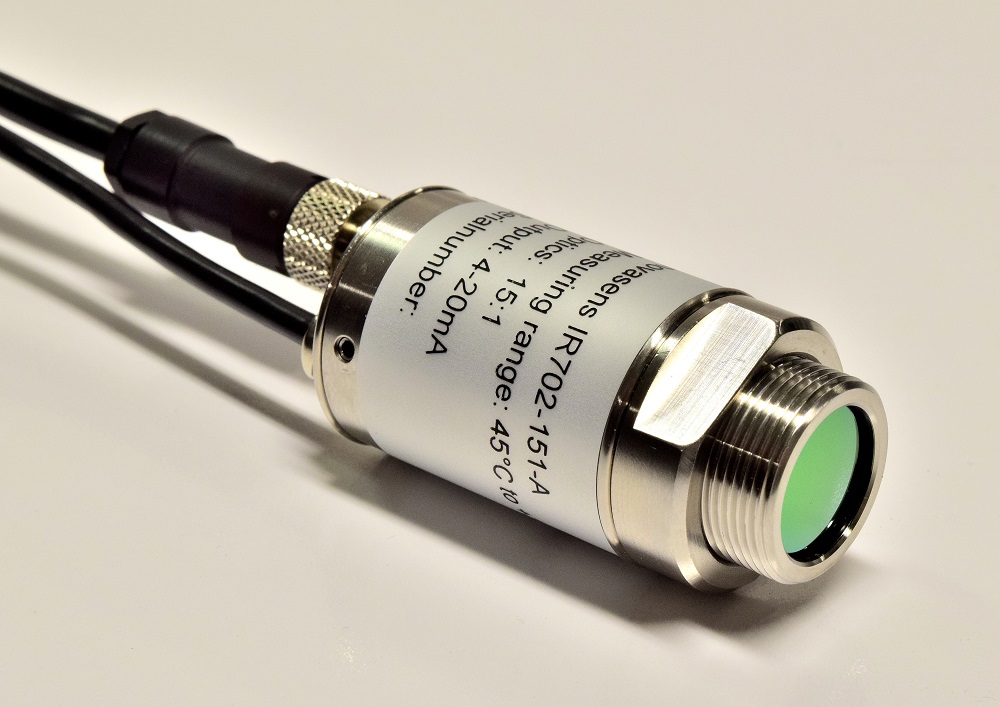
The advantages of using infrared pyrometers compared to conventional contact sensors:
– No influence on the surface of the measured object
– Simple and easy operation
– no wear and tear as with contact probes
– cost-effective measuring device
– Fast temperature measurement in the millisecond range
– Temperature measurement on hot measurement objects or on measurement objects that are electrically live.
Areas of application for pyrometers
– Temperature detection of food
– Control of temperatures in production
– Temperature monitoring for quality control
– Temperature measurement in molding and tempering processes