Monitoring the application of hotmelt adhesive when bonding corrugated cardboard boxes
In modern industrial production, the precise application of hotmelt adhesives plays a decisive role in the quality and efficiency of products. Hotmelt adhesives are used in particular in the production of corrugated cardboard boxes. Folding elements of the cartons are glued together and the structure of the cartons is stabilised. Precise, error-free application of the adhesive is essential to ensure high product quality. This applies to both the mechanical stability of the carton and its durability during transport and storage.
By using the novasens 2000 hotmelt controller, it is possible to precisely monitor and control the adhesive application. The controller works on an infrared basis and measures the heat radiation of the applied hotmelt adhesive. This technology allows the application quantity to be precisely determined, ensuring consistent quality and reducing errors.
This article explains how such hotmelt controllers are used specifically in cardboard production and what advantages they offer in terms of quality assurance and increased efficiency.
Application example: Monitoring the hotmelt adhesive quantity during adhesive application when gluing cardboard boxes
One example from practice is the production of shipping cartons consisting of several layers of corrugated cardboard. Here, the hotmelt adhesive is applied either as a line or as a dot application to firmly bond the cardboard walls together.
A manufacturer of packaging solutions uses the novasens 2000 hotmelt application controller to ensure that the hotmelt adhesive bead is applied evenly.
For MCS 400/m2 cardboard, a bead of adhesive 100mm long and 2.0mm in diameter is applied to each of two sides of the cardboard. The adhesive is applied at approx. 160°C, the feed rate is approx. 0.5m/sec.
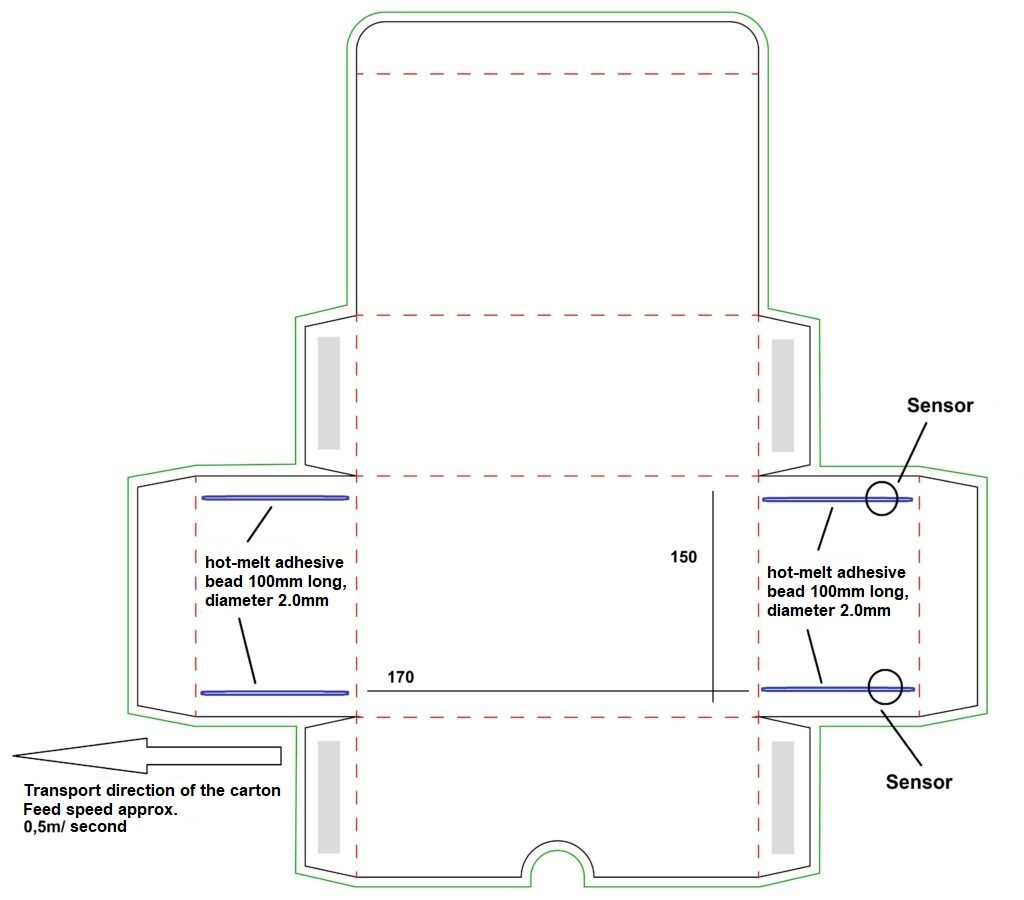
The adhesive application is monitored by the novasens 2000 hotmelt controller, which uses infrared radiation to measure the amount of adhesive applied. The controller recognises whether the amount applied is sufficient to ensure a strong bond. Only as much adhesive is used as is necessary.
Thanks to this precise measurement, the manufacturer was able to achieve material savings of up to 10% and at the same time increase production speed by 15%. Defective gluing was reduced by 20% and production waste was significantly reduced.
Advantages of quality assurance with the novasens 2000 hotmelt application controller:
If the amount of adhesive is not optimised, mechanical and aesthetic problems can occur. Too less adhesive means that the cardboard elements are not sufficiently bonded together. This considerably impairs the mechanical strength of the carton’s bonding. The carton can fall apart, especially with heavy goods or during prolonged storage or transport.
On the other hand, excessive adhesive application not only leads to unnecessarily high material costs, but also has an impact on the flexibility and processability of the carton. Excess adhesive can ooze out when the carton is folded or closed and contaminate the machine and products. This would lead to additional cleaning work and possible complaints.
The consistently high quality of the gluing process helps to minimise product defects and increases efficiency and customer satisfaction.
One major advantage is the material savings. The hotmelt controller precisely measures and controls the amount of adhesive applied, preventing excessive amounts of adhesive from being applied. This can reduce adhesive costs by up to 10%-15%. Using the novasens 2000 hotmelt controller therefore ensures that sufficient adhesive is applied and reliable bonding is guaranteed.
In addition to material savings, the precise control also helps to save time. Automated monitoring of the adhesive application means that product lines can run faster, manual checks are not necessary and faulty production interruptions are minimised. In many cases, the production speed can be increased by up to 20%.
How the novasens 2000 hotmelt application controller works:
The novasens 2000 hotmelt application controller works by precisely measuring the heat radiation of the applied hotmelt adhesive. This process is carried out using infrared sensors that measure and monitor the temperature of the adhesive as it is applied to the material. Hot melt adhesive cools down relatively quickly after application, which is why accurate real-time measurement is crucial to reliably determine the amount of adhesive applied.
The sensors are calibrated in a way that they recognise the specific heat radiation of the Holtmelt and filter out external interference factors such as ambient light or external heat sources. The controller can precisely determine the amount of adhesive and make immediate corrections in the production process in the event of deviations. This real-time monitoring enables consistent adhesive application quality, which is important for the mechanical strength of the bond as well as for material efficiency.
The adhesive quantity is measured in the range of 0-250% and the measured quantity is put out in an analogue standard sensor output signal in the range of 0-10VDC to be forwarded to the PLC. Here the adhesive nozzles are then controlled to apply more or less adhesive.
Compared to other measuring methods, such as optical monitoring, infrared technology has the advantage of working independently of the speed of the production lines or the colour of the applied adhesive. Even under varying production conditions, the production process remains stable and consistent.
In addition, the novasens 2000 hotmelt application controller can be integrated into existing automation systems, which further improves process control and enables complete documentation of the adhesive application for quality assurance purposes.
Conclusion:
Using the novasens 2000 hotmelt application controller in corrugated box production offers significant advantages for process control, quality assurance and increased efficiency. The precise measurement of the adhesive application quantity on an infrared basis ensures that the optimum amount of hotmelt is applied, which leads to material savings and minimize production waste.
A Fault-free adhesive application in production is of key importance for the stability and quality of the end products, especially in the production of cardboard packaging for the logistics and packaging industry. Companies benefit from higher production speeds, less manual intervention and better resource management.
The integration of the hotmelt application controller into existing production lines optimises automation. The consistent, documented quality of the adhesive application leads to a significant reduction in production costs, improved quality of the end products and therefore increased customer satisfaction.